Orchestrating the daily production of 100 tons of ice cream
Froneri Switzerland
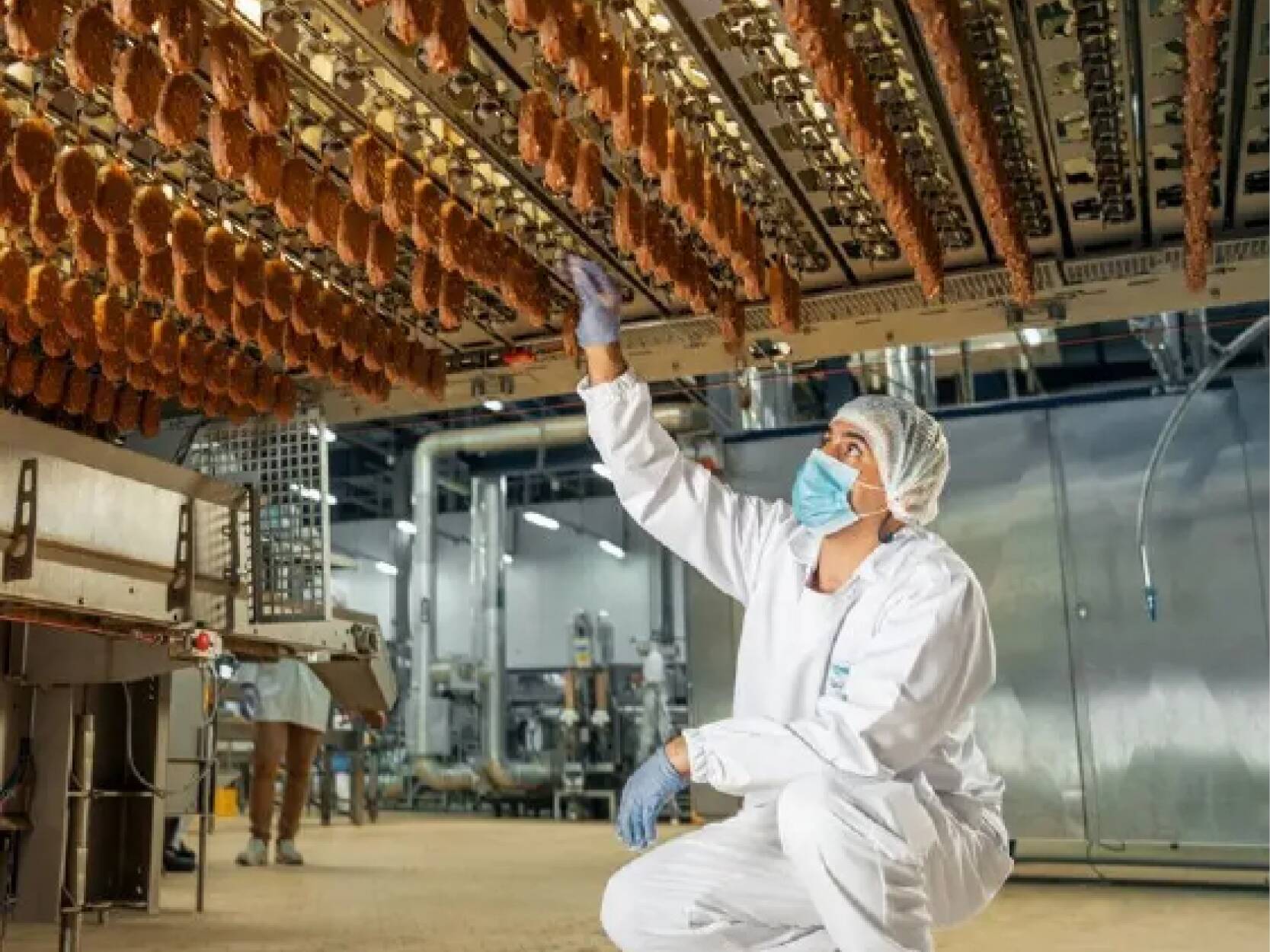
The challenge - low level of automation and insufficient range of functions
The roots of Froneri Switzerland go back to 1886, when RoCo began producing preserved food in Rorschach. in 1942, the business was finally expanded under Nestlé with the production of frozen food and then Frisco ice cream. Nestlé's takeover of the Mövenpick quality ice cream brand in 2004 enabled the company to develop into a genuine Swiss ice cream icon. In 2016, Froneri was created from the merger of Nestlé ice cream with R&R, with the aim of becoming the world's leading ice cream company.
Based on this company history, Froneri has used the existing automation and software solution from Nestlé times for many years. In order to modernize production and remain competitive, the existing solution had to be replaced - the level of automation had to be increased and the functionalities expanded.
The implementation with iDIP - production according to recipe
To ensure that the replacement of the outdated systems met Froneri's needs as closely as possible, we worked closely with the project manager, the relevant specialists and users. The following main functions were implemented in compliance with regulatory requirements:
- Mapping the Froneri processes: Thanks to the flexibility of iDIP, the processes could be mapped without compromise.
- Production planning: Production planning is supported with iDIP. Data from the Order Management System (OMS) flows directly into production planning.
- Production monitoring: By integrating machines, iDIP also ensures that production is monitored.
- Recipe management: iDIP communicates the recipe data to the control system, which ensures that the correct ingredients, quantities etc. are used in the production process.
- Storage connection: iDIP ensures that there is feedback to the storage system regarding the ingredients used, quantities, etc.
- Compliance with specifications from the food industry: iDIP can be used to map specifications that need to be taken into account.
- Allergen testing: iDIP also ensures allergen testing in the production process.
- Track & Trace: Track & Trace ensures that it is always clear which material was used in which batch.
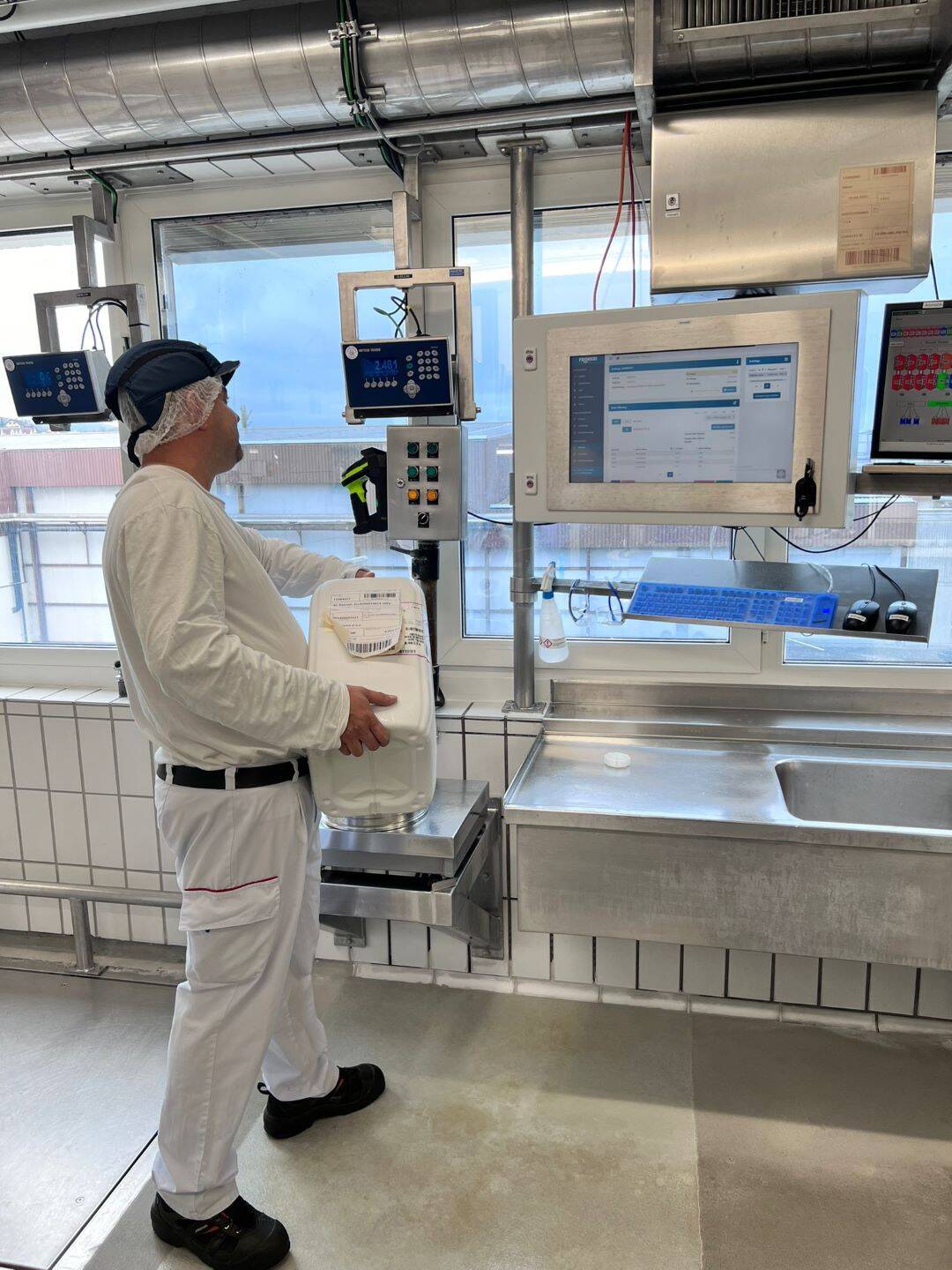
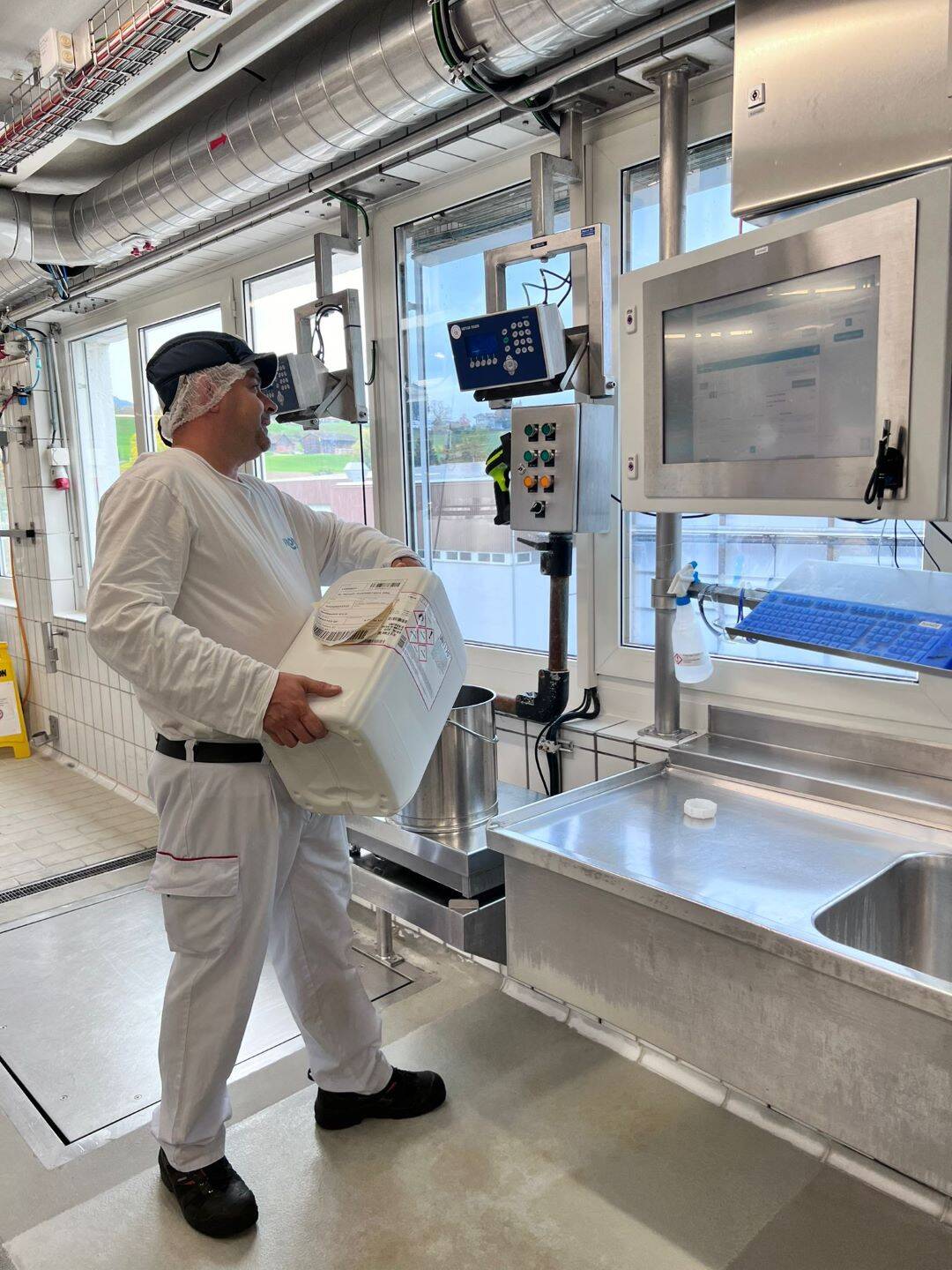
The result - a stable, expanded production process
Froneri was able to replace the legacy system inherited from the merger, introduce a future-oriented solution and ensure the continuation of the complex processes without any problems. The high quality of the automation solution guarantees that production can continue to be monitored and the production history can be tracked - it is always possible to trace which ingredients were used for an individual product, where they came from, who supplied them, etc. In addition, the verification of specifications and allergy-related risks is also ensured.
At the same time, the stability of the production process has been significantly improved compared to the previous solution; frequent shutdowns are no longer necessary. Furthermore, the integrated batch planning helps to better control the occupancy of tanks and prevent multiple occupancy.
"Thanks to the iDIP power tool, we have our production firmly under control. It's impressive how this software solution can successfully manage everything from batch management to system control, workstation support, Track & Trace and Visu. It makes work fun!"
Patrick Mendler, Head of Technology
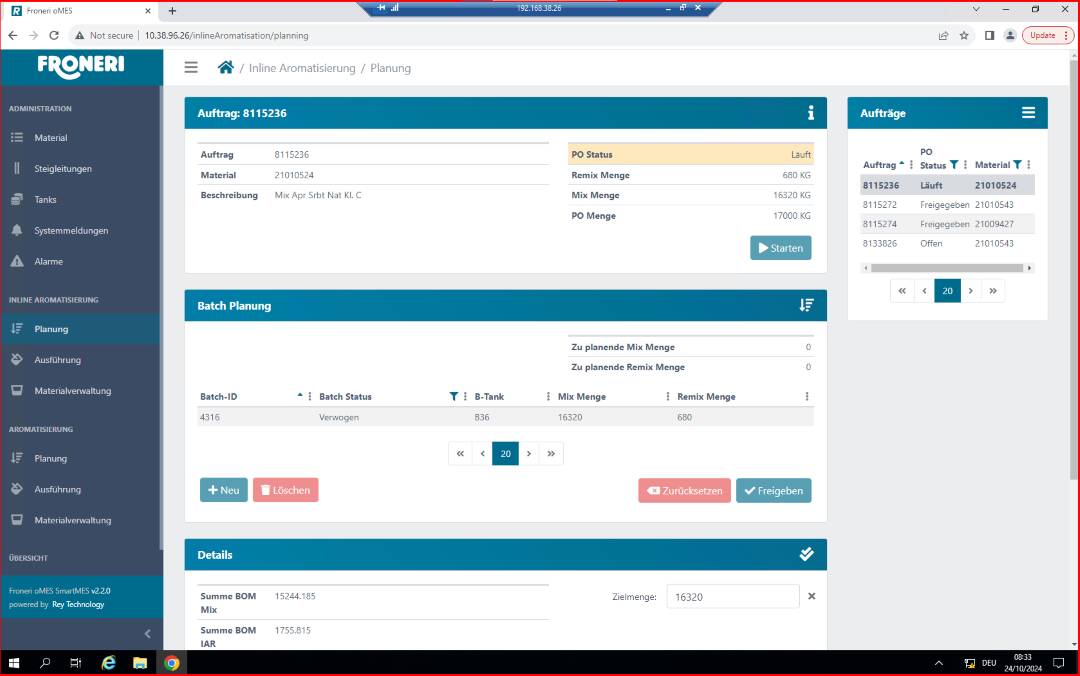
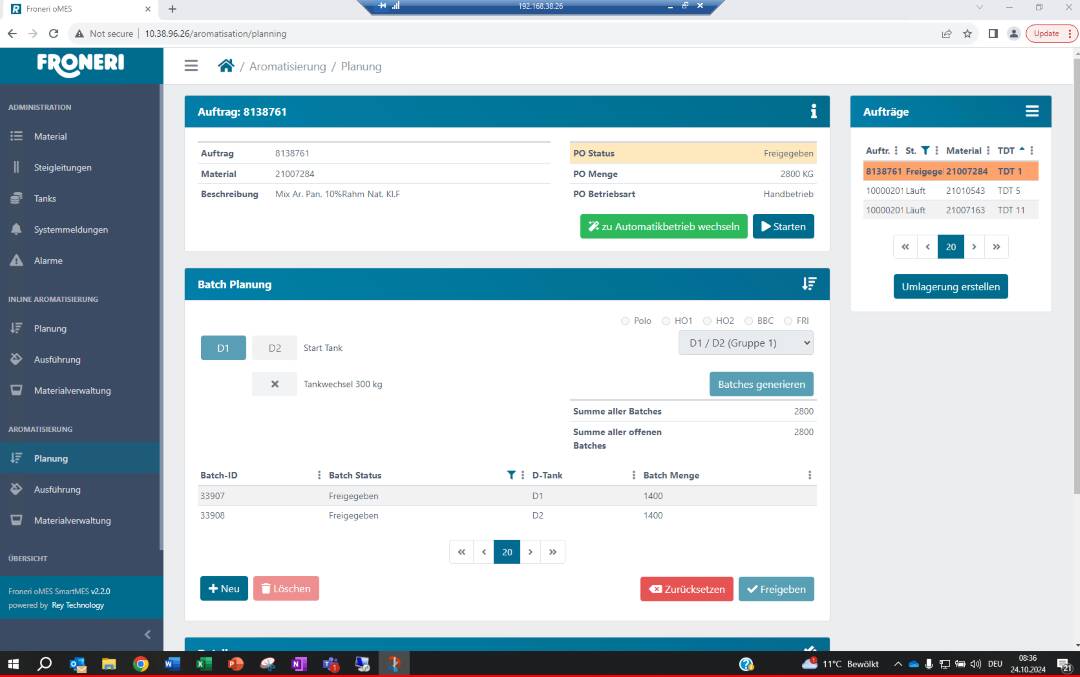
Just start
Get to know the Smart Factory solution of the future! We would be happy to show you the benefits you can achieve in your company
Tomy Mändli
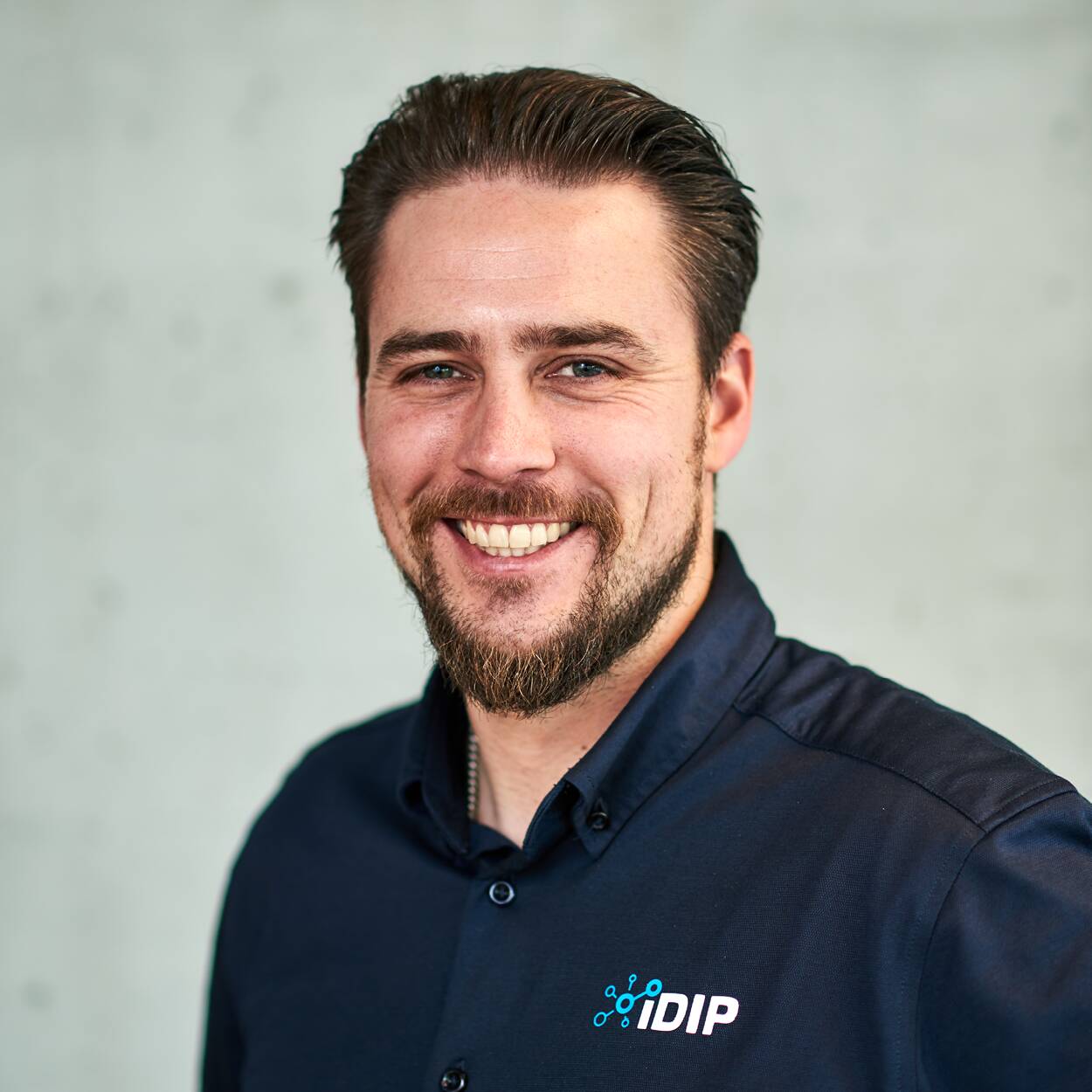