Continuous process optimization in production
V-ZUG
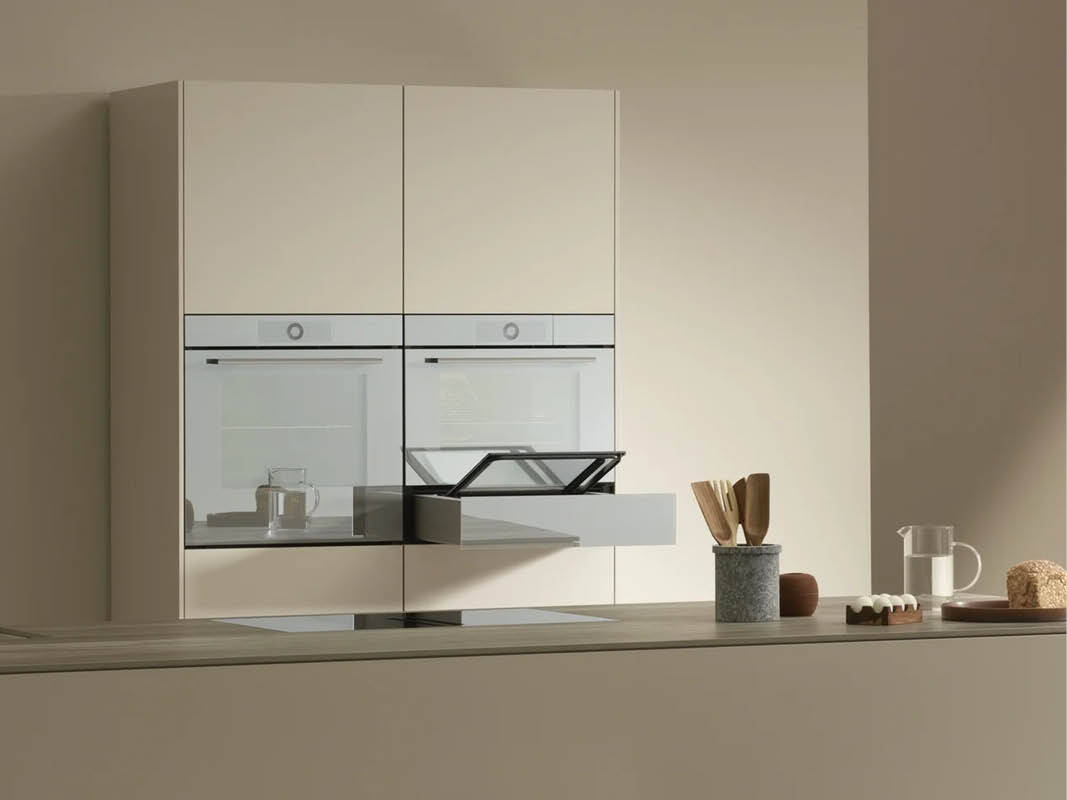
The challenge - increasing efficiency, quality assurance and flexibility
Founded in Zug in 1913, V-ZUG develops, creates and produces appliances that bring lightness to the home and creativity to the kitchen. With the responsible and climate-neutral production of high-precision and durable products, V-ZUG is committed to a sustainable future.
In the course of continuous improvement, V-ZUG strives, among other things, to reduce manual handling and, if this is still necessary, to fully support employees in production.
Furthermore, V-ZUG wants to gain a better understanding of the aspects that influence the quality of a product for quality assurance purposes and thus continuously improve production processes. Finally, ongoing adjustments and optimization of the production lines and workstations mean that changes to the systems used are always necessary.
Implementation with iDIP - step-by-step and comprehensive process optimization in production
The following main functions were introduced in connection with the continuous improvement and further digitalization of production:
- Order management: Orders are retrieved via SAP, processed and displayed at the semi-automated assembly workstations or used for order processing at the fully automated workstations. Feedback is also sent to SAP via iDIP.
- Assembly workstation: The digital assembly workstation shows employees the assembly instructions and guides them through the assembly process (with images, checkpoints, parts lists, etc.).
- Recipe management: The machine recipes for controlling the systems and machines are managed in the iDIP.
- Teams integration: Notifications are sent directly to the internal Teams channel.
- Machine connection: The machine connection is used to log work processes with MDE and automate entire production lines.
- FTS/AGV connection: Autonomous vehicles and driverless transport systems are controlled and coordinated via iDIP.
- High-bay warehouse integration: The new high-bay warehouse was connected to iDIP. iDIP manages goods storage and retrieval.
- Pick-by-light: The storage containers are equipped with intelligent lights that light up as soon as the components they contain are required for the current order or work step.
- Track-and-trace: events in production (e.g. downtimes, machine defects, etc.) are recorded and assigned to the serial numbers of the products produced during this period to ensure clear traceability.
The result - central production digitization for independent further development
More than 100 assembly workstations have been digitized so that employees are guided through the assembly process individually for each workstation with optimal support. Pick-by-light provides them with even better support, which makes their work easier and reduces errors
Thanks to track-and-trace, in the event of quality defects or complaints, the serial number can be used to trace whether an event took place during production. Knowing this contributes to overall quality improvement.
The configuration of the processes and the machine connections can be created, adapted and optimized independently by the plant managers.
"With the help of iDIP, we increase efficiency, quality and employee satisfaction in our SmartFactory on a daily basis, and we can even do it ourselves."
Adrian Theiler, COO
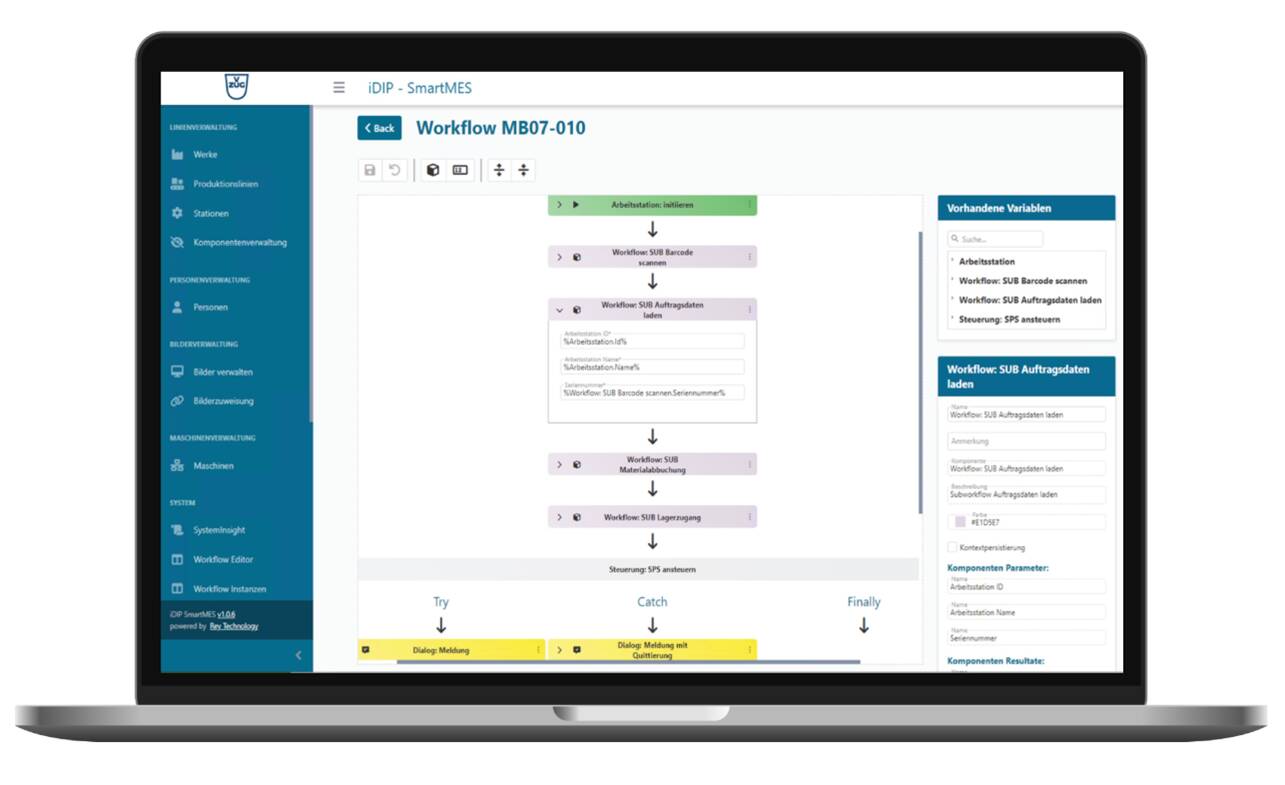
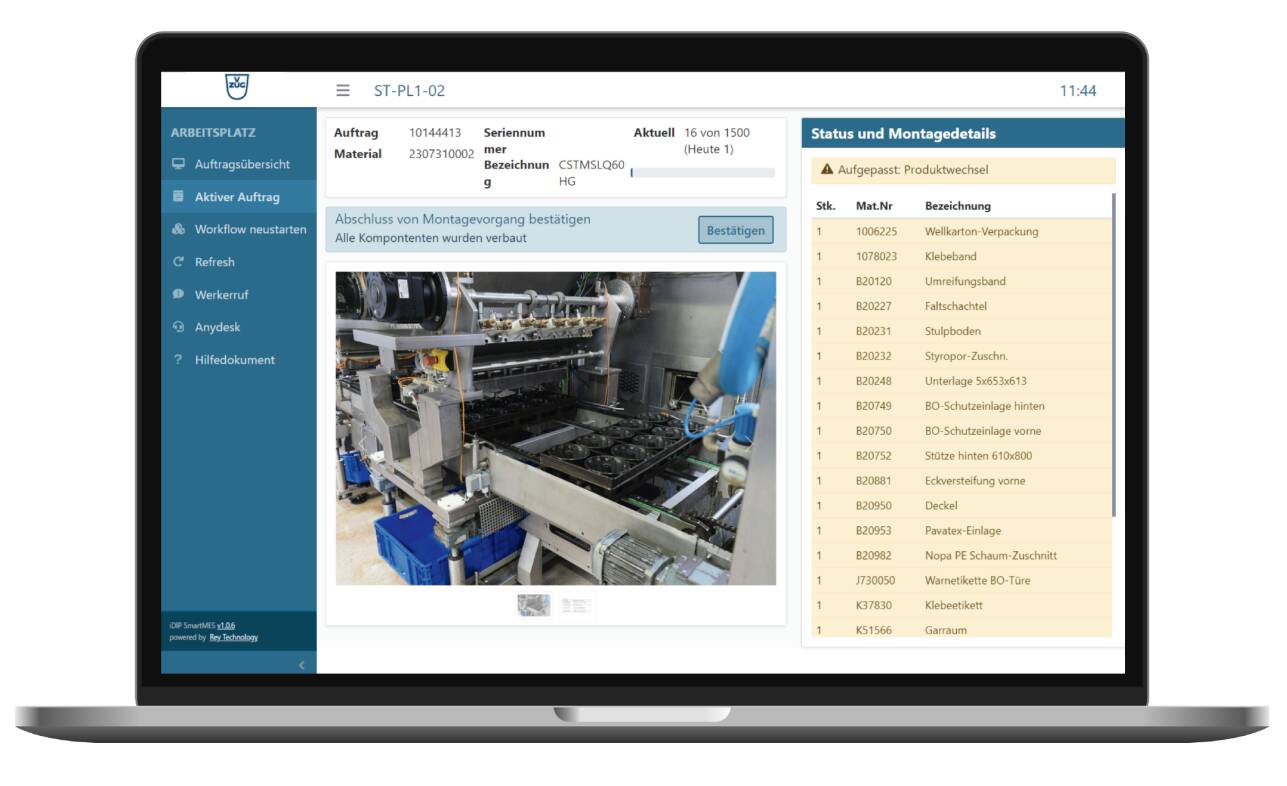
Just start
Get to know the Smart Factory solution of the future! We would be happy to show you the benefits you can achieve in your company
Tomy Mändli
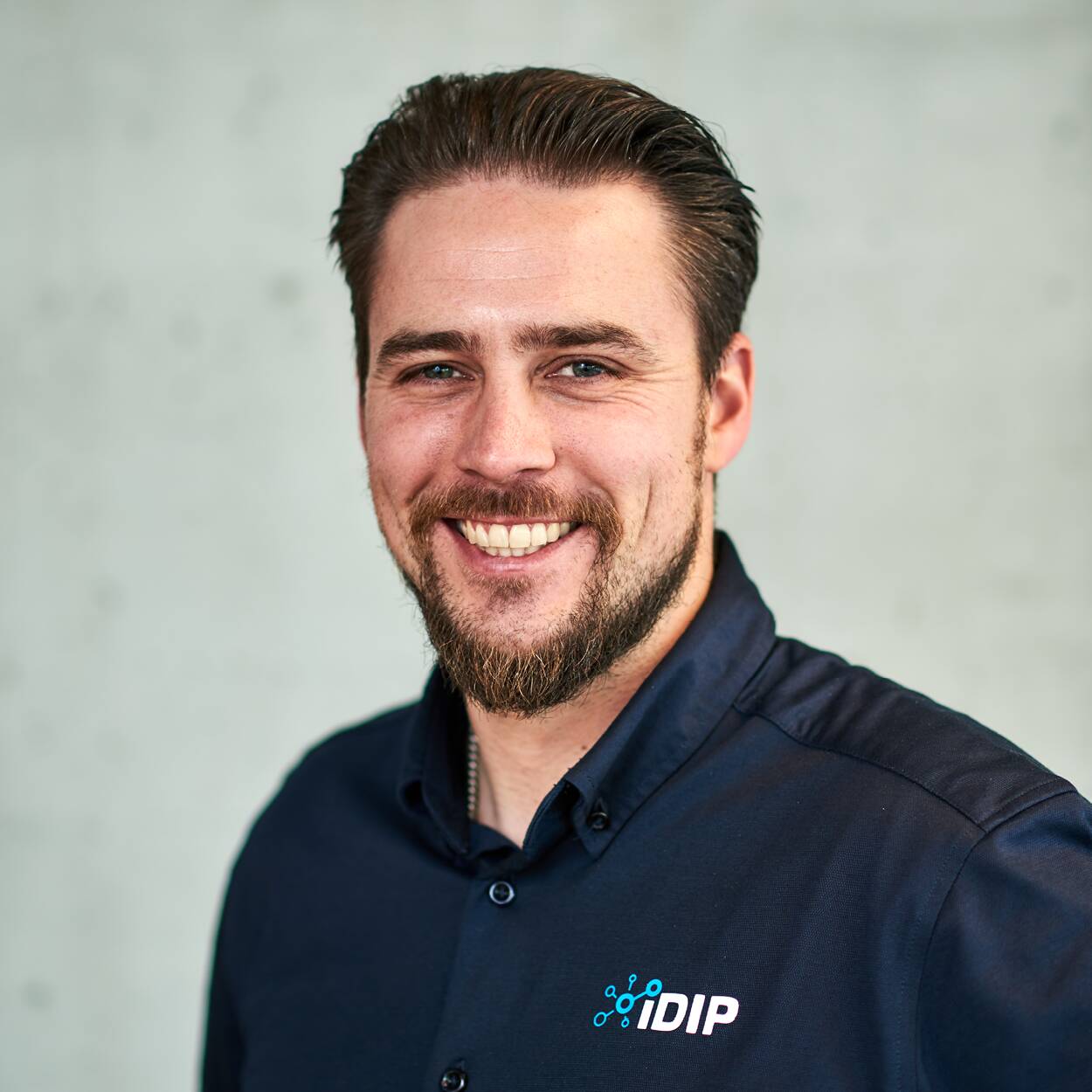